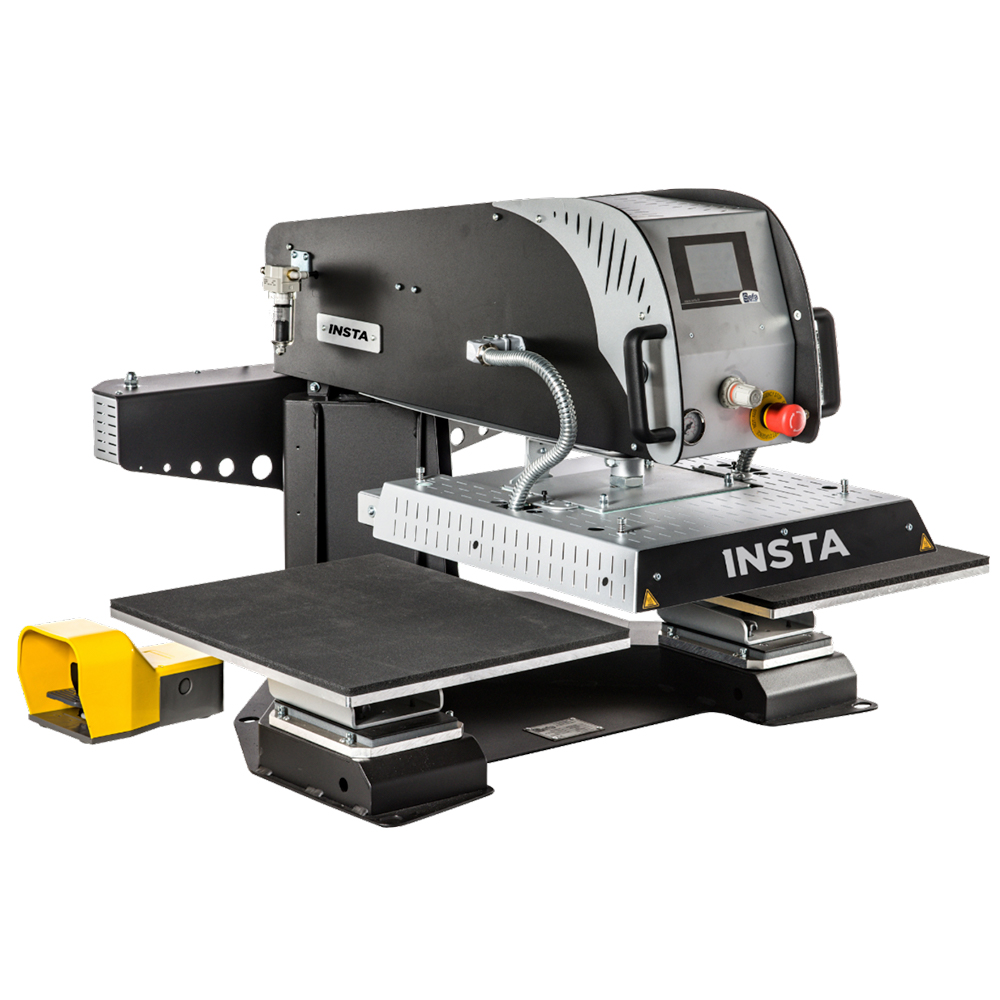
Direct-to-Film (DTF) printing has quickly become one of the most exciting techniques in custom printing, offering exceptional versatility, vibrant colors, and durable results. Whether you’re a hobbyist looking to expand your skills or a professional printer adding a new service to your lineup, understanding the right equipment is key to success. In this blog, we’ll cover the essential tools you need to get started with DTF printing, including printers, heat presses, and other must-have items.
DTF Printer: The Core of Your Setup
Your DTF printer is the heart of your printing operation, responsible for creating the high-quality images that will eventually be transferred onto your chosen material. However, not just any printer will work for DTF printing. You’ll need a specialized printer capable of handling the unique ink requirements and film that DTF printing relies on.
Types of Printers for DTF Printing
- Converted Inkjet Printers: One common approach to DTF printing is using a converted inkjet printer. These printers, often repurposed from popular brands like Epson, are modified to work with DTF inks, which include white ink for opacity. Inkjet printers offer high-resolution prints, ensuring your designs are crisp and detailed.
- Commercial DTF Printers: If you’re serious about starting a professional DTF printing business, consider investing in a commercial-grade DTF printer. These machines are specifically built for DTF printing, meaning you won’t have to worry about the modifications that come with converting an inkjet printer. They also tend to have higher production speeds and better durability for long-term use.
Key Features to Look For in a DTF Printer
- Print Resolution: The higher the resolution, the sharper and more vibrant your designs will be. Look for printers that offer at least 1440 dpi for professional results.
- White Ink Management: Since white ink is essential for creating a solid base for the colors to stand out, choose a printer with a reliable white ink management system to avoid clogging.
- Roll vs. Sheet Printers: Some printers allow you to print on rolls of DTF film, which can be more efficient for bulk printing, while others are designed for individual sheets. Choose the one that best fits your workflow.
Heat Press: The Transfer Specialist
Once your design is printed on the DTF film, it’s time to transfer it onto fabric or another surface. This is where the heat press comes in. The heat press applies the right amount of heat and pressure to bond the design to the material, ensuring a lasting, high-quality finish.
Types of Heat Presses
- Clamshell Heat Press: The clamshell model is one of the most common heat presses used for DTF printing. It opens and closes like a clamshell, making it compact and easy to use. This press is ideal for small to medium-sized prints but may be challenging for thicker garments due to the limited space between the platens.
- Swing-Away Heat Press: In a swing-away model, the upper platen swings to the side, allowing more space to lay your material. This design gives you more control over garment placement and is better for thicker items like hoodies or jackets.
- Draw Heat Press: Draw heat presses have a pull-out lower platen, allowing you to prepare your garment on the lower platen without being directly under the heat. This option is great for avoiding accidental burns and improving precision in garment alignment.
Key Features to Look For in a Heat Press
- Temperature Control: Consistent and adjustable temperature control is essential for DTF printing. Look for a press that can reach temperatures between 320°F and 350°F (160°C to 180°C), the typical range for DTF transfers.
- Pressure Adjustment: Having adjustable pressure is crucial because different materials may require different levels of force to achieve a perfect transfer. A heat press with easy-to-modify pressure settings will give you more versatility.
- Size of Platen: The size of your heat press platen should match the typical size of your transfers. Standard sizes range from 15×15 inches to 16×20 inches, but larger presses are available for bigger projects.
Other Essential Tools for DTF Printing
While a DTF printer and heat press are the big-ticket items, there are several other important tools you’ll need to complete your setup and achieve professional-grade results.
DTF Transfer Film
This is the medium on which your design is printed before it’s transferred to the fabric. DTF film is specially coated to handle the unique properties of DTF inks. It’s essential to use high-quality DTF transfer film to ensure that the ink adheres well and transfers properly to your material.
There are two main types of DTF film:
- Cold Peel Film: With cold peel, you’ll need to wait for the transfer to cool completely before removing the film, which can take a bit longer but usually results in a slightly softer feel on the garment.
- Hot Peel Film: Hot peel film allows you to remove the film while it’s still warm, speeding up production. Many printers prefer hot peel because it saves time and works well on most fabrics.
DTF Inks
DTF printing requires specially formulated inks that can adhere to both the film and the fabric once transferred. The ink set typically includes cyan, magenta, yellow, black (CMYK), and white. The white ink layer is critical for creating the opaque base that ensures vibrant colors on any fabric color, especially dark ones.
Powder Adhesive
After printing your design onto the DTF film, you’ll need to apply a powder adhesive, which helps bind the ink to the fabric. The powder is sprinkled onto the printed film and then cured by heat, usually with a heat gun or an oven. It’s important to ensure an even application of the adhesive powder for consistent results.
Curing Oven or Heat Gun
To set the adhesive powder onto the DTF film, you’ll need to cure it. A curing oven provides even heating and can process multiple transfers at once, making it a good option for high-volume production. For smaller-scale operations, a heat gun can also work, though it may be more time-consuming and less consistent.
Optional, but Useful Add-ons
- Pretreatment Machines: While not always necessary for DTF printing, some materials (especially hard surfaces like wood or glass) may benefit from a pretreatment that helps the design adhere better.
- Cutting Tools: Scissors or precision cutting tools will help you trim excess film from around your design for a clean, professional look.
- Teflon Sheets: These non-stick sheets can be placed between your transfer and the heat press platen to protect the press and ensure even heat distribution.
Setting Up Your DTF Printing Space
Before you dive into DTF printing, you’ll need to ensure you have a well-organized and properly ventilated workspace. DTF inks and adhesives can emit fumes during curing, so good ventilation is a must. Additionally, having a clean, dust-free environment is important for keeping your prints and transfers pristine.
The Right Equipment for the Right Results
DTF printing is an exciting method that opens up a world of possibilities for custom designs on a wide variety of materials. By investing in the right equipment—like a reliable DTF printer, a high-quality heat press, and essential accessories like transfer film and adhesive powder—you’ll be well on your way to producing professional-grade prints. Whether you’re printing for fun or starting a business, understanding the tools you need is the first step to DTF printing success.