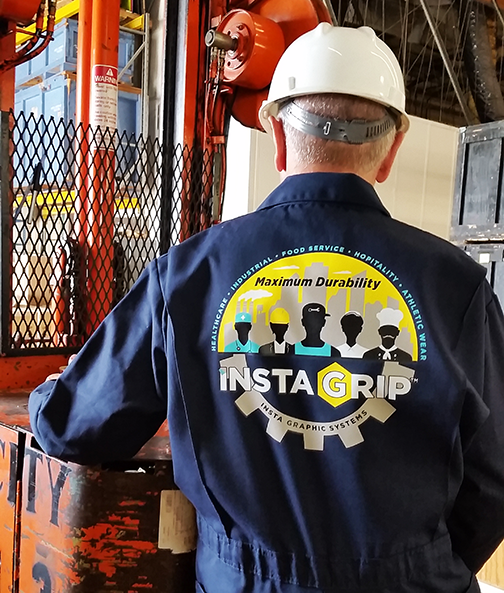
In an article published by Impressions magazine, Chris Pluck shares with us some of his knowledge on heat transfer technology.
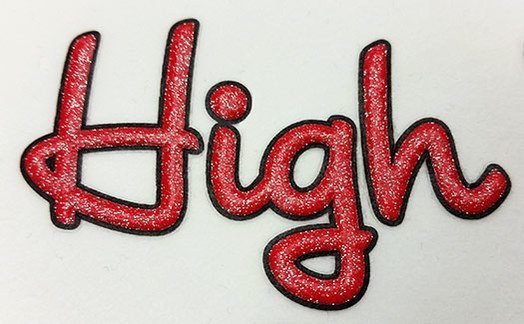
Heat transfers are produced by printing transfer ink onto a substrate transfer paper or film. Once the ink has been applied to the substrate, it is then gelled under a dryer. The finished transfer is then pressed onto the garment and, once applied, the final product is ready to wear.
Using heat transfers can be advantageous to a direct textile screen printer because they eliminate the possibility for misprints, which can result in garments being rejected. Such mistakes can be costly because the ink is applied to the most expensive part of the overall product: the garment. Alternatively, heat transfers can help keep printed product rejects to a minimum.
With an array of transfer inks available, there are many finishes and textures to suit each fabric type. Transfers can produce soft, yet durable printed images. In some instances, they can compete with — or even beat — the hand of screen-printed graphics. When printing short print runs or samples, transfers can provide an easy way to get quick-turn images to customers, who can then apply them to garments.
Following are four things you need to know about heat transfers.
1. Differentiation from Screen Printing: Textile screen-printing inks are applied directly onto a garment or fabric surface, then immediately cured under a dryer. When the printing and curing are completed, the garment is ready to wear. With transfers, multiple designs can be printed simultaneously. Once completed, the transfer sheet can be cut into single transfers, packed and sent off site for application to garments.
Heat transfers can be printed singly or as multiple graphics and don’t need to be applied to garments until necessary.
This means the transfer customer can choose from a range of “stock” transfers and wait to purchase the garment until required.
Applying transfers to multiple garments is a clean and efficient process, as the transfer should be pressed onto the garment in a sterile environment away from the print shop.
2. Formula for Success: It is important to know in advance the fabric type to which you will applying a transfer. Every fabric has its differences, so you must understand that no one transfer type is a good fit for all fabrics. For example, if a garment has a high degree of fabric dye migration or high stretch and elasticity, it must be paired with a transfer type that will enable the transfer and fabric to work harmoniously.
Another important factor for successful transfer application is a quality heat press that has a proven track record of success with various garment types. It must be well made and able to successfully reproduce controlled temperature and pressure parameters during the transfer-application process. These features may mean the difference between a lasting transfer or a reject.
With the introduction of large-format heat presses, allover transfers now can easily be heat pressed onto garments to produce stunning visual images.
3. Special Effects and Textures: Glitter, shimmer, metallic and other shiny finishes can be produced to enhance a transfer’s design. Embossed transfer images are available to create 3-D effects, as well as faux leather and suede finishes.
Combinations of transfer flat ink, and special-effects and textured ink, can easily be used in a single transfer print to produce super finishes. Multiple surface finishes, which are important to the visual look, feel and texture of the finished transfer image, also can be aligned with each transfer graphic concept.
Some of the best glitter, metallic and shimmer graphics can be produced using transfers, as the transfer paper used with these shiny inks usually is a high-gloss type, which in turn provides the same gloss effect to the glitter or shimmer once applied to the garment.
Other special effects, such as phosphorescent glow-in-the-dark and puff embossed images, also are available to use for transfers.
Sublimation and offset transfers also can be produced. Depending on the ink type, they can help to create photorealistic graphics or spot-color design finishes that can be used in sports numbers, lettering, corporate logos and tagless labels, to name a few.
4. Transfers for Workwear: One of the latest innovations involves heat transfers for industrial workwear or garments that need to withstand rigorous laundering processes. These types of transfers are capable of resisting high-temperature washes and — in some cases — up to 50 industrial wash cycles. They make it possible to imprint uniforms and workwear that traditionally have been embellished with embroidery or appliqués, thus significantly shortening the turnaround cycle.
In addition, the use of these durable transfers goes beyond apparel, gracing such items as backpacks, canvas bags and more.
If you haven’t tried printing your own transfers or using them to customize garments, give it a shot. You may find that it perfectly complements your current product offering.
Chris Pluck, business development director for Insta Graphic Systems, has been in the imprinted textile industry for more than 30 years. He has a background in screen printing and offset lithography technologies, and was instrumental in establishing inventive heat-fusible printing products and print application methods. For more information, visit instagraph.com.