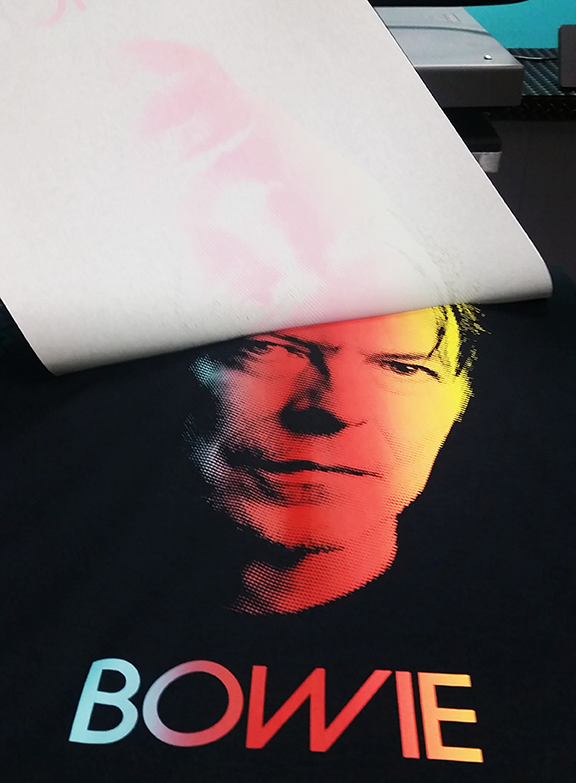
Heat transfers are printed on specially prepared transfer substrate paper and films. Find out more from this article by Chris Pluck, recently published in Printwear:
There are three standard types of transfer substrate paper and/or polyester transparent films that are used with inks to create transfers. Depending on the type of paper/film used, the transfer created will be either a hot-split, hot/warm-peel or cold-peel transfer. These three substrates will, in turn, conform to variable heat press, temperature settings when heat applying the transfer to the garment.
Here are three standard types of transfer application methods:
Hot-split Transfers:
The paper/film substrate is uncoated or only partially coated (transfer release coating) so that the transfer ink cannot easily peel from the paper when placed under the heat press.When the heat press has finished hot pressing the transfer onto the garment, the transfer paper is immediately removed from the ink. This allows approximately 40 percent of the ink to stay on the paper while the remaining ink is pressed onto the garment. Because of the split action of the ink during the transfer application, this process of transfer ink and paper combination is called hot-split.
Once applied to the garment the hot-split ink has a soft finish as the transfer ink is now pressed down into the fibers of the fabric without producing an ink film surface which would increase the hand-feel finish.
Hot / Warm-Peel Transfers:
The substrate paper/film suitable for these types of transfers has a semi-release coating on the surface. This coating allows for a little amount of the ink to stay back on the paper/film substrate during the heat press application. The hand-feel of the hot/warm-peel transfer is usually not as soft as the hot-split transfer version; however, the finish will be smooth overall.
Once the heat press application of the transfer has taken place, the substrate paper/film is immediately removed from the ink.
Cold-Peel Transfers:
A cold-peel transfer is named such because when the transfer ink is heat pressed onto the garment it is allowed to cool for a number of seconds before it is peeled completely from the substrate paper. This leaves 100 percent of the ink on the garment. Because of the cold-peel application, the finish of the transfer has more surface hand-feel than either the hot-split or hot-peel transfer versions. Thus, when creating heat transfers, it is important to understand the interaction between the transfer ink carrier substrate, the transfer ink itself and the transfer application method when the transfer is applied to the fabric.
No one heat transfer type will suit all applications, so knowing more about a transfer’s fusible attributes, the application function, and method can bring you closer to achieving a successful transfer-to-garment result at the first try.
Chris Pluck, business development director for Insta Graphic Systems, has been in the imprinted textile industry for more than 30 years. He has a background in screen printing and offset lithography technologies, and was instrumental in establishing inventive heat-fusible printing products and print application methods. For more information, visit instagraph.com.